Known for their exceptional strength and versatility, neodymium magnets have become a staple material in industries ranging from electronics to automotive applications. However, many consumers and manufacturers often wonder why these magnets are so expensive and what they are made of. This article takes an in-depth look at the composition of NdFeB permanent magnets, focusing specifically on the different types of NdFeB, including Chinese bonded NdFeB, pressed NdFeB magnets, and injection molded NdFeB magnets.
Composition of NdFeB magnets
NdFeB magnets, neodymium iron boron magnets, are mainly composed of three elements: neodymium (Nd), iron (Fe) and boron (B). The unique combination of these materials gives the magnet a high magnetic field strength, making it one of the most powerful permanent magnets available today.
The typical composition of NdFeB magnets can vary, but a common formula is about 30% neodymium, 60% iron, and 10% boron, with trace amounts of other elements (such as dysprosium or praseodymium) added to improve performance and thermal stability. The addition of these elements can significantly affect the properties of the magnet, including its resistance to demagnetization and temperature stability.
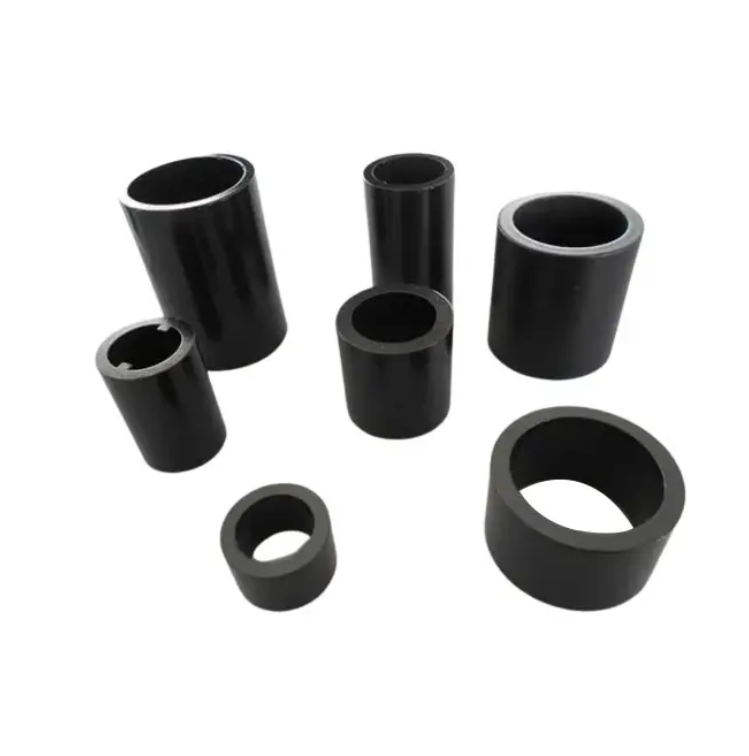
Why are neodymium magnets so expensive?
The cost of neodymium magnets can be attributed to several factors:
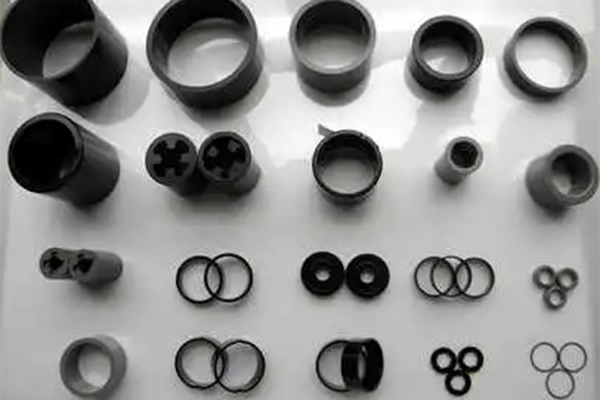
Raw Material Cost: Neodymium is a rare earth element, and its mining and processing require a lot of labor and are expensive. The supply of rare earth elements is concentrated in a few countries, with China being the largest producer. The supply and price fluctuations of these materials directly affect the cost of neodymium magnets.
Manufacturing Process: The production of NdFeB magnets involves complex manufacturing processes, including sintering, bonding and processing. Each step requires specialized equipment and skilled labor, which adds to the overall cost. For example, pressed NdFeB magnets are made by pressing powdered materials and then sintering them at high temperatures, a time-consuming and energy-intensive process.
Quality Control: Ensuring the quality and performance of neodymium magnets is critical, especially in applications where reliability is critical. Rigorous testing and quality assurance processes increase manufacturing costs.
Market Demand: In recent years, with technological advancement and the widespread use of electric vehicles, renewable energy systems, and consumer electronics, the demand for neodymium magnets has surged. This high demand can lead to higher prices, especially if supply chains are disrupted.
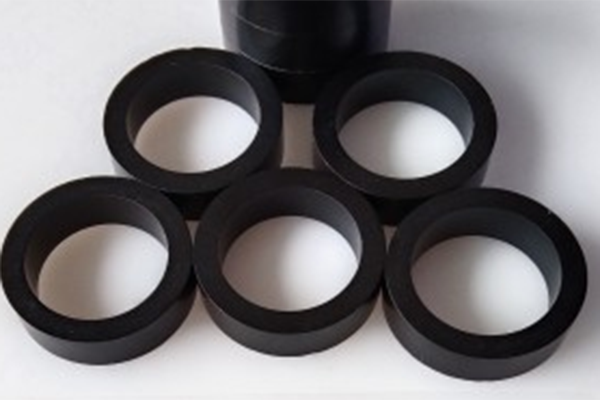
Types of NdFeB magnets
China Bonded NdFeB Magnets: These magnets are made by bonding NdFeB powder with polymer resin. The bonding process can produce complex shapes and sizes that are difficult to achieve with traditional sintering methods. China is a major producer of bonded NdFeB magnets, leveraging its abundant supply of rare earth materials and advanced manufacturing capabilities. These magnets cost less than sintered magnets, making them ideal for a variety of applications.
Pressed NdFeB Magnets: Pressed magnets are made by pressing NdFeB powder into the required shape and then sintering it. This method produces dense and strong magnets, but the manufacturing process is more labor-intensive and requires precise control of sintering conditions. Pressed NdFeB magnets are commonly used in applications requiring high magnetic strength, such as motors and generators.
Injection Molded NdFeB Magnet: This type of magnet is made by injecting a mixture of NdFeB powder and polymer into a mold. The process enables high-volume production and the manufacture of complex shapes with tight tolerances. Injection molded magnets are particularly useful in applications where weight and size constraints are critical, such as the automotive and aerospace industries.
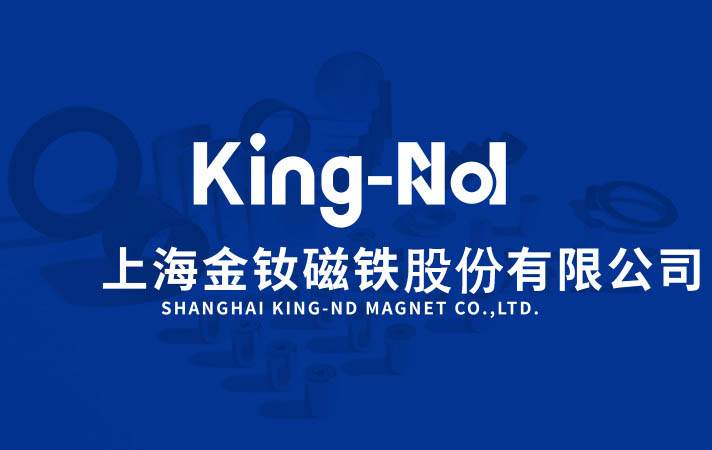
In summary
Neodymium magnets, especially Chinese bonded NdFeB magnets, pressed NdFeB magnets and injection molded NdFeB magnets, play a vital role in modern technology. Their high strength and versatility make them indispensable in a variety of applications. However, the cost of these magnets can be high due to scarce raw materials, complex manufacturing processes, and high demand.
Understanding the composition and types of NdFeB magnets can help consumers and manufacturers make informed decisions when choosing the right magnet for their needs. As technology continues to evolve, demand for neodymium magnets is likely to grow, prompting continued innovation in production methods and materials, which may help reduce costs in the future.
Post time: Jan-21-2025